ARUM
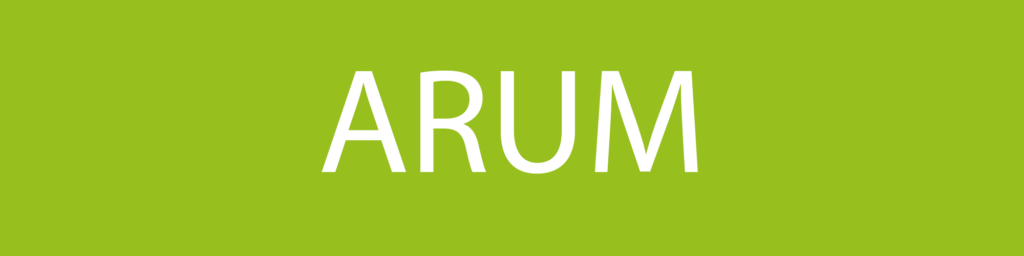
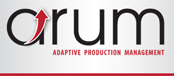
Adaptive pRodUction Management
Duration: 9/2012 – 9/2015 Funding: FP7
Partners: EADS, Airbus, Certicon, Iacobucci Group, Modular Galley Systems, TIE Kinetix, Smart Solutions, Cologne University of Applied Sciences, Voith Aerospace, University of Manchester, IPB, ICCS, CVUT, FernUniversität Hagen
ARUM
The ARUM project aimed to improve planning and control systems for the manufacturing of complex, small-lot products, such as aircraft, aircraft interiors, and ships. Producing aircraft is incomparable to producing large-quantity products such as cars or computers. A car manufacturer makes a relatively small investment in design and production ramp-up (the phase between designing a prototype and smooth production of the final product line), compared to the number of cars it eventually sells. A company like Airbus faces a similar investment, even though it will only sell a small number of aircraft of the same design. Ships and aircraft are often produced in batches as small as 3 to 5, or are even completely customized. Small-lot manufacturers thus need ICT solutions and tools to speed up their learning curve, allowing a smoother transit from design to production. They simply cannot learn from mistakes at the beginning of a series, but must get it right on the very first model.
ARUM resulted in an intelligent Enterprise Service-Based platform (i-ESB). The platform consisted of a service-based architecture with a knowledge-based Multi-Agent System. The i-ESB platform gathers information from sources such as sensors and resource management systems, giving decision makers and planners better insight into and control over the design-to-production process. Also, time-, cost- and risk-analysis takes place within the platform. The project had a double approach, making use of both prediction (in the pre-planning phase) and real-time control (in the production phase).
Contribution
Within the project, Almende's main focus was on the multi-agent-based event simulation and visualisation tools for self-organized distributed multi-project scheduling of manufacturing processes, resulting in the MIDAS (manufacturing incident detection and simulation) toolkit. MIDAS collects statistics of incidents during the production process. It analyses the manufacturing process and handles disruptive events during the ramp-up phase. We developed the software tool especially for this project, based on our tools, Eve and vis.js.
Results
The project improved our expertise on building planning and simulation systems based on multi-agent frameworks, applied to practical settings where there was little opportunity to iterate over multiple production runs as lot sizes were small, which required highly advanced prediction and simulation models.
More info?
Need specific information regarding the project? Please contact our senior consultant for more information.
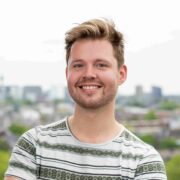